Der Mehrwert digitaler Steuerungen und Sensorik steht seit Langem außer Frage. Offene Standards, flexible Schnittstellen und leicht zu bedienende Interfaces sorgen nun dafür, dass sich diese immer mehr durchsetzen, verrät Jürgen Kitzler, Automation Sales Engineer bei der Weidmüller GmbH.
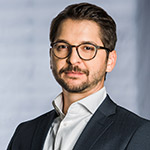
Jürgen Kitzler
Automation Sales Engineer der Weidmüller GmbH
©Weidmüller GmbH
Wie verändert die Digitalisierung die Steuerung von Maschinen?
Es ergeben sich dadurch sehr viele neue Anwendungsgebiete und Möglichkeiten. Es muss nicht jede Berechnung oder Datenablage innerhalb einer speicherprogrammierbaren Steuerung geschehen. Durch effiziente und flexible Schnittstellen können aber einfacher denn je Daten extern verarbeitet oder gespeichert werden. Früher dauerte es mitunter einige Jahre, bis neue IT-Technologien in der Industrie verankert und verwendet wurden. Heute kann man die rasante Verringerung dieser Übergangszeiten quasi in Echtzeit miterleben. Selbst diejenigen, die Digitalisierung noch vor einiger Zeit als Selbstzweck abgestempelt haben, erkennen mittlerweile den Wert von Daten und den Nutzen von Webtechnologien.
Wie reagiert Weidmüller auf diese Entwicklung?
Weidmüller versucht hier ein klares Bild zu zeichnen, das auch für versierte Techniker und Spezialisten zu verstehen ist, die ihren Ursprung nicht unbedingt in der IT haben. Die Hardware ist der erste Schritt, um die Möglichkeiten von IoT zu implementieren. Dabei setzen wir unter anderem auf unsere bewährte Remote-I/O-Lösung „u-remote“ mit all den Möglichkeiten, die sich durch die Vielfalt der digitalen und analogen Ein- und Ausganskarten sowie Sonderfunktionsmodule ergeben: Darunter fällt die Einbindung von Wiegezellen, Encodern, seriellen Modbus-Teilnehmern und vielem mehr. Wir beginnen also bei den Rohdaten der Automatisierung und bieten einen Weg, der diese Daten mit einem industriellen Hardwareansatz und in wenigen Schritten für IoT-Anwendungen nutzbar macht. Der dezentrale Ansatz hilft unter anderem den anlagenweiten Datenverkehr zu verringern und somit auch die Störungsanfälligkeit im Netzwerk zu reduzieren. Dieser Ansatz lässt sich beispielsweise durch unsere Steuerung „u-control web“ von kleinen, einfachen Maschinen mit integrierten Automatisierungsaufgaben bis hin zur Datenaufbereitung von komplexen Prozessanlagen skalieren.
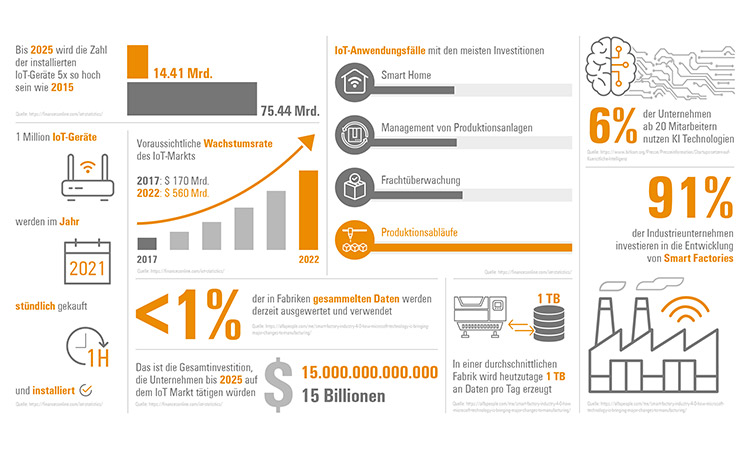
Warum hat man sich für die webbasierte Anbindung der Steuerung entschieden?
Der webbasierte Ansatz macht vieles einfacher: Ein sicherer Fernwartungszugriff ist ohne großen Aufwand möglich. Wartungsaufgaben oder auch kleine Änderungen lassen sich ganz einfach mit dem Handy oder Tablet unterstützen. Proprietäre Schnittstellen gehören der Vergangenheit an und Kompatibilitätsprobleme mit Betriebssystemen oder Engineering Tools anderer Hersteller gibt es somit nicht mehr. Man ist außerdem nicht in einem Systemkäfig gefangen. Durch offene Standards lassen sich die Vorteile einer großen IT- und Automatisierungstechnik-Community nutzen und sofort anwenden. Aber auch die Integration in bestehende Systeme ist kein Problem. „NodeRed“ ist hier ein umfangreiches und nützliches Werkzeug, um eine gemeinsame Plattform zu schaffen.
Wie kann man Daten nutzen, um Steuerung und Betrieb zu optimieren?
Wir verwenden beispielsweise unsere eigens entwickelten Vibrationssensoren, um mittels Bluetooth-Low-Energy-Verbindungen das Vibrationsverhalten eines Elektromotors an unsere „u-control web“ zu senden. Die Daten werden darin vorverarbeitet, in ein kompatibles Format gebracht und in eine Datenbank – lokal beim Kunden oder als Cloudservice – übermittelt. Von dort können Machine-Learning-Modelle auf die Daten zugreifen und Vorhersagen treffen oder Rückschlüsse ziehen. Diese Modelle sind entweder mit unserem Data-Science-Team im Zuge eines Projektes entstanden oder der Kunde erstellt mithilfe unseres Automated-Machine-Learning-Tools seine eigenen Industrial-Analytics-Modelle.
Was hat der Kunde davon?
Wartungs- und Service-Tätigkeiten können durch den Webzugriff schneller durchgeführt werden, durch den sichtbaren Zustand der Maschine kann die Wartung effizienter geplant werden. Der Einsatz von KI eröffnet viele Möglichkeiten. Von vorausschauender Wartung von Motoren über prädiktive Qualitätsanalysen von Schweißverbindungen bis hin zur dynamischen Prozessoptimierung in den verschiedensten Produktionsumgebungen ist Weidmüller bereits erfahrener Player am Markt. Auch die Erweiterung von Geschäftsmodellen hin zum Verkauf von Maschinenverfügbarkeit ist eines der Anwendungsfelder. Die „Weidmüllerlösung“ kann also vom Sammeln von Rohdaten bis zum ML-Modell reichen.